Multinational enterprises have a lot to gain by treating their factory workers well, according to new research by Provost Richard Locke P’18 and his former student, Greg Distelhorst, now an assistant professor of global economics and management at the Massachusetts Institute of Technology.
The study, published in the American Journal of Political Science, shows that on average, factories that enforce basic labor and environmental standards benefit from a $1.6 million increase in annual purchases.
Furthermore, when factories improved their compliance, their orders increased by an average of four percentage points, which roughly translates to $110,000.
These findings were especially “pronounced in the apparel sector,” which faces more social pressure from consumers to comply with labor and environmental standards than others, said Mark Anner, associate professor of labor and employment relationships at Pennsylvania State University, who is unaffiliated with the study.
“Activists can make it painful to be noncompliant,” Distelhorst told Phys.org.
Despite this correlation, there is a lack of incentives for factories to enforce such conditions, Locke said. “Many of the actors involved in the supply chain have mixed incentives,” he said. Most of “the governments and countries where many of these companies are located … have really terrific labor and environmental regulations, but they don’t enforce them.” Roughly 80 percent of the companies in their study were non-compliant.
Sometimes, a country avoids enforcement because it doesn’t have the resources to inspect factories, enforce the working age or hold companies accountable to the legal minimum wage. Other times, countries fear that enforcement will increase the cost of doing business and drive out buyers, Locke explained.
“We show that compliance does pay, but it may not pay enough. Maybe 4 percent is just not attractive enough of a benefit to bring factories up to that level of compliance,” Distelhorst said.
Locke and Distelhorst carried out the study by “rigorously analyzing a novel data set on export transactions and social compliance audits of over 2,000 supplier factories,” Anner said.
These audits are measures taken by companies to ensure that their suppliers adhere to a specific code of conduct, including labor and environmental regulations that often vary from country to country, Locke said. In these audits, outside inspectors visit factories, interview managers, review employees’ time cards, examine factory records and inspect factories for adherence to health and safety regulations, Distelhorst said.
The researchers obtained the data set from a global sourcing agent, which takes orders from companies and helps them identify and handle transactions with factories, Distelhorst explained. For some factories, such as Nike, obtaining records took years, Locke added.
Both Locke and Distelhorst wanted to “find ways to reconcile a world that’s, for better or for worse, dominated by market capitalism,” Distelhorst said. “That should not come at the expense of dangerous or abusive conditions of workers.”
Going forward, the researchers would like to know why the majority of factories remain non-compliant despite its demonstrated benefits.
For Locke, continuing his research and teaching is essential, even as provost. Though he balances his responsibilities “with great difficulty,” it’s “important for a university administrator to still have his fingers on the pulse of what universities are all about,” he said.
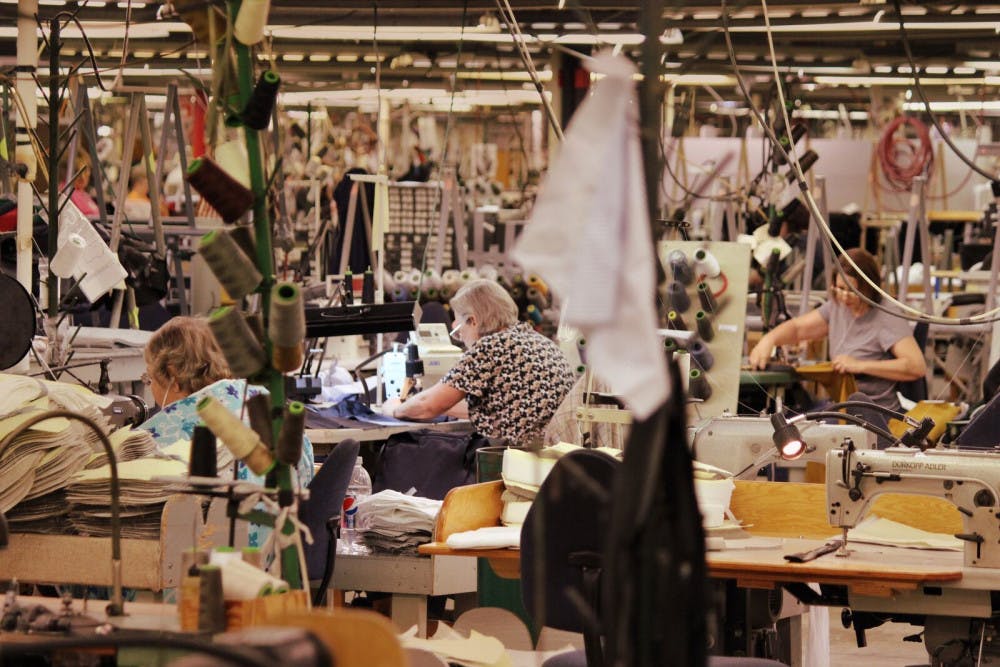
ADVERTISEMENT
More